NaOH Solution: Benefits of Vertical Integration in the Pharma Supply Chain
In today’s fast-moving world, businesses need reliable supply chains to keep things running smoothly. This is especially true for essential materials like Sodium Hydroxide (NaOH) solutions.
NaOH solution plays a critical role in pharmaceutical manufacturing processes. Including in buffers, excipients, and clean-in-place systems. These solutions ensure safety, consistency, and compliance, which are essential for producing high-quality pharmaceuticals.
A strong pharma supply chain ensures consistent product quality, timely delivery, and adherence to regulatory standards. But when supply chains fail, they can lead to costly delays, inconsistent materials, and even compliance risks.
One proven way companies solve these challenges is by vertically integrating their product offering. By producing raw materials in-house, businesses gain better control over the supply process. This means more reliable products, stronger quality control, and reduced risk.
What Is NaOH Solution and Why Does It Matter?
Sodium Hydroxide liquid solutions, also called caustic soda, are essential in pharmaceutical supply chains. Manufacturers typically produce liquid solutions from National Formulary (NF) grade sodium hydroxide pellets. This ensures they meet strict U.S. and European Pharmacopeia (USP and EP) requirements.
Unlike solid NaOH pellets, liquid solutions are ready to use. Reducing the need for additional preparation and minimizing risks such as dust exposure.
Versatility makes NaOH solution invaluable across the pharmaceutical industry. Here’s how they are used:
- Buffer Solutions: NaOH is used to prepare buffers, ensuring a stable pH environment for sensitive formulations.
- Clean-in-Place Systems: NaOH cleans and sanitizes equipment in pharmaceutical manufacturing facilities, maintaining hygiene and compliance.
- Chemical Reagents: NaOH is used to produce active pharmaceutical ingredients (APIs) for many medications.
- Inactive Ingredients (Excipients): NaOH acts as an excipient in drugs like pain relievers and anticoagulants, ensuring stability and effectiveness.
The ability to create these solutions on demand is a major advantage of in-house integrations. It reduces dependency on third-party suppliers and ensures a steady supply.
Challenges in the Pharma Supply Chain
Even with the best planning and management, pharma supply chains face unique challenges. These challenges can disrupt production, drive up costs, and put product quality at risk. Here are some of the key issues businesses encounter:
Inconsistent Quality
When companies rely on third-party suppliers, the quality of materials can vary from batch to batch. For industries like pharma, where precision is essential, even small inconsistencies can lead to much bigger consequences. Variations in purity, concentration, or contamination levels can lead to:
- Delays in production as materials are re-tested or replaced.
- Non-compliance with strict regulatory standards, putting product safety at risk.
- Financial losses from wasted materials or rejected batches of finished products.
Delays and Shortages
Supply chains are often long and complex, involving multiple suppliers and logistical challenges. This makes them vulnerable to disruptions caused by:
- Shipping Delays: Global transportation bottlenecks can slow down the delivery of essential raw materials.
- Raw Material Shortages: Fluctuations in global demand or geopolitical events can make it harder to secure enough supply.
- Regulatory Hurdles: Stricter rules and standards can delay shipments or increase the time it takes to approve new suppliers.
These delays slow down production. They also affect customer delivery times, raise costs, and lower overall efficiency.
Rising Costs
Third-party suppliers often add significant costs to raw materials including:
- Handling and packaging.
- Transportation and storage.
- Currency and tariff fluctuations for imported materials.
Over time, these added costs can make it harder for manufacturers to remain competitive.
Sustainability Pressures
The demand for greener practices is growing rapidly. Consumers, investors, and regulatory bodies are all pushing for companies to adopt more sustainable processes. For the pharma industry, this means:
- Reducing the carbon footprint of supply chains.
- Cutting down the amount of waste generated during raw material production and transportation.
- Meeting stricter environmental regulations to stay compliant and competitive.
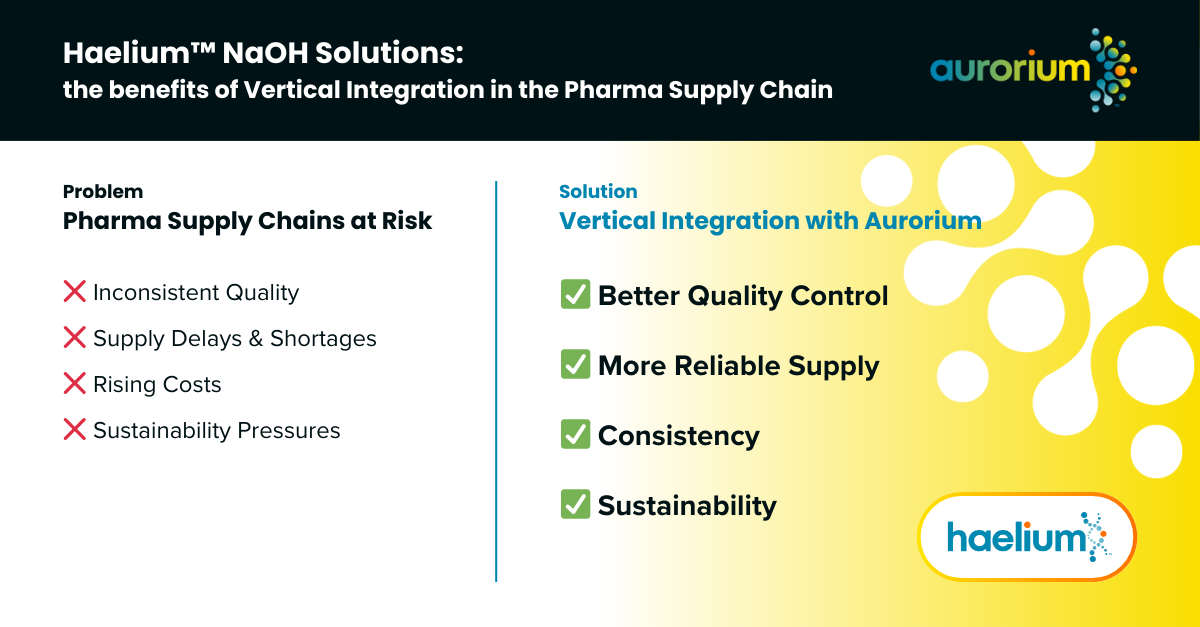
How Vertical Integration Solves These Challenges
A strategy where companies produce the raw materials they need, rather than relying on external suppliers. This approach helps manufacturers address common challenges in their supply chain, delivering clear benefits:
Better Quality Control
When producing their own NF and EP NaOH pellets, manufacturers maintain strict control over quality. Manufacturers should monitor every step of production. Ensuring each batch of pellets, water quality, and solutions, meet the highest standards for purity and consistency. To follow the strict regulations, you need precise and reliable materials.
Vertically integrated offerings minimize risks such as contamination or variability that can occur when sourcing materials from third-party NaOH pellet suppliers.
More Reliable Supply
Lengthy supply chains often face disruptions caused by global shipping delays, material shortages, or unexpected price increases. In-house integration eliminates reliance on third-party NaOH pellet suppliers, giving manufacturers greater control over their supply.
By producing NaOH solutions and pellets in-house, companies can:
- Respond quickly to changing demand.
- Avoid production delays caused by external disruptions.
- Ensure materials are always available, even during global supply chain challenges.
This reliability allows businesses to meet production timelines consistently, supporting both operational efficiency and customer satisfaction.
Greener Practices
Sustainability is a growing priority across industries, and backward integration supports eco-friendly initiatives. By controlling production processes, manufacturers can implement greener practices that reduce waste, lower energy use, and minimize their overall environmental impact.
Examples of sustainable actions include:
- Reducing greenhouse emissions and carbon footprint when making raw material in house (versus transporting overseas).
- Reducing packaging waste by producing and delivering materials more efficiently.
These practices align with sustainability goals for pharma companies while improving production efficiency, making businesses more attractive to environmentally conscious customers and regulators.
Dependable Consistency
Better quality control, reliable supply, flexible products, and greener practices make backward integrated product offerings stronger. This helps every part of the supply chain. Companies like Aurorium are leading by offering high-quality NaOH solution from raw material produced on-site.
Vertical integration strengthens the entire manufacturing process, not just individual products. Pharma ingredient manufacturers benefit greatly from this approach, allowing them to create high-performance materials. Tailored to the needs of the pharmaceutical industry in a sustainable and dependable manner.
Aurorium is a trusted pharma ingredient manufacturer and leverages in-house manufacturing processes to provide the highest quality materials for its customers.
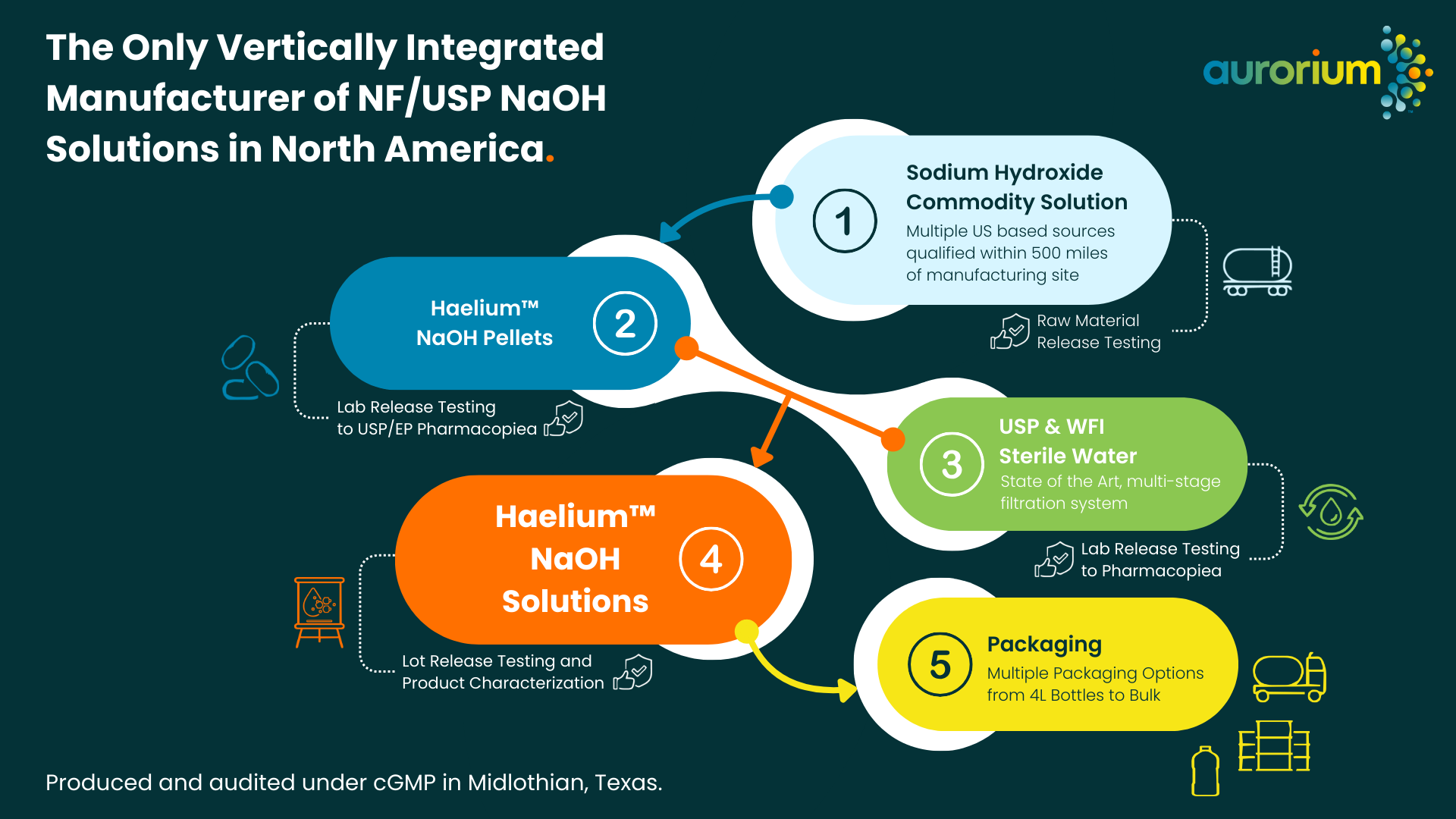
Aurorium: A Vertically Integrated Manufacturer of NaOH Solution
Aurorium produces NaOH pellets in various standards, including NF, EP, ACS, and JP. They also make high purity (USP and Water For Injection) water on site. Producing USP and EP grade NaOH Solution - Sodium Hydroxide Liquid for the pharmaceutical industry. The processes at our Midlothian, Texas site run under Current Good Manufacturing Practices (cGMP) and are audited frequently.
By maintaining control over every step of the production process, Aurorium ensures consistent quality, dependable supply, and compliance with industry standards.
We are focused on building a stronger, more reliable pharma supply chain. As a leading specialty chemicals and pharmaceutical excipient manufacturer, we deliver high-quality products tailored to your business needs.
Consistent supply, superior quality, and a commitment to greener manufacturing practices make Aurorium your ideal specialty solutions partner. Aurorium is here to support your success and meet your goals with confidence! Whether you need pellets, solutions, or other customized Pharma Ingredient solutions.